Wie es zur Anschaffung einer CNC-Fräse kam
In den 1990er Jahren schaffte ich (beruflich bedingt) den ersten Computer an. Das blieb, von Laptops abgesehen, bis heute der einzige Kauf eines Computers. Erst wurde aufgerüstet und irgendwann der erste PC komplett aus Komponenten selbst zusammengebaut. Beim PC-Gehäuse gab es 2012 einen ersten Eigenbau. Als die ersten (teuren) lüfterlosen PC-Gehäuse auftauchten beschloss ich ein solches selbst zu bauen. Die Teile aus Alu dafür wollte ich anfertigen lassen. Der Preis war bei kleinen Stückzahlen aber zu hoch.
Das führte zu der Idee, eine CNC-Fräse anzuschaffen und die Teile selbst zu fertigen. Die Wahl fiel auf die Pro-Basic H 06/05 von MechaPlus. Die Maschine wird komplett montiert auf einer Palette angeliefert. Der Zufall wollte, das ich noch einen alten Laptop T61 hatte, mit Express-Card-Slot. Ein Express-Card Parallelport Adapter war im Internet schnell gefunden, doch halt, eine Kundenbewertung sagte: für CNC Steuerung ungeeignet. Beim Adapter von StarTech.com fand sich dann die gegenteilige Aussage: CNC Steuerung geht!
MechaPlus hatte die Kabel der Schrittmotoren so beschriftet, dass die Länge des Arbeisbereichs von 600mm die Y-Achse und die Breite von 500mm die X-Achse darstellten. Ein Anruf bei der Firma ergab, das sei so richtig, die Endschalter wären entsprechend angebracht. In meinen Zeichnungen war bei den Teilen aber die lange Seite (z.B. 400mm) der X-Wert und die Breite (z.B. 280 mm) der Y-Wert. Ich entschloss mich die Kabel zu tauschen und musste dazu an der Spindel der quer verlaufenden (neuen) Y-Achse den Endschalter verlegen.
Die Mecha 06/05 noch ohne Arbeitsplatte
Verlegung des Endschalters der Y-Achse
Anbringung des neuen Endschalters auf der anderen Seite
Der Laptop mit Linux CNC
Das Steuergerät MechaPlus 3S
Der Express-Card Parallelport Adapter
Gesamtansicht des Arbeisbereichs
Gesamtansicht der Arbeisplatte
Die Mecha H 06/05 mit dem StepConf-Wizard von LinuxCNC einrichten
LinuxCNC StepConf Dialog zur X-Achse
LinuxCNC StepConf Dialog zur Y-Achse
GCode erstellen
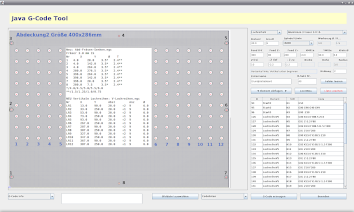
LinuxCNC zur Steuerung der Fräse zu nutzen war von Anfang an klar. Wie der GCode erzeugt werden sollte war dagegen nicht so leicht zu beantworten. Es gibt Programme, die aus CAD Zeichnungen den GCode erstellen, doch CAD Zeichnungen hatte ich nicht. Deshalb erstellte ich ein Java-Programm, um meine Zeichnungen mit den Koordinaten anzeigen und diese Werte in entsprechende Felder eingeben zu können. Daraus wurden dann mit eigens geschriebenem Java-Code die GCode-Zeilen erzeugt. Zum Testen (Simulieren) der so erstellten GCode-Dateien installierte ich das auch für Linux erhältliche Camotics und für Schriften das Python-Programm F-Engrave.
Das Java-GCode-Tool entstand schrittweise und der erzeugte G-Code wurde an der Fräse getestet. Wenn etwas geändert werden musste, wurde umprogrammiert. Zum GCode-Tool und dem Java-Code gibt es eine PDF ⇒⇒
Das Fräsen der Grundplatte
Das Video zeigt das Fräsen der Grundplatte. Mit einem 2mm Einschneider werden die Löcher zur Befestigung Ø 3.5mm und die Löcher für das Fräsen der Gewinde Ø 2.5mm gefräst.
Danach folgt das Gewindefräsen. Die Gewindefräser für 3mm Gewinde von Sorotec haben nur einen 1mm dünnen Schaft, da darf nichts schiefgehen. Der GCode für das Fräsen und für das Gewinde wird getrennt programmiert, da kann ein Tippfehler beim Eingeben der Werte teuer werden.
Zuletzt werden mit einem 3mm Einschneider die Lochreihen für die Zuluft gefräst. Am Schluss des Videos sehen wir die fertige Grundplatte.
Frontplatte und Rückseite
Zum Fräsen der schmalen Frontplatte und Rückseite wird ein Alublech 2mm stark in gleicher Größe wie die Grundplatte verwendet. Mit einem 2mm Einschneider werden zuerst wieder die Befestigungs- und Gewindelöcher gefräst.
Danach folgen die Aussparungen in der Frontplatte, die mit einem 3mm Einschneider bei voller Zustellung gefräst werden. Da es getrennte GCode-Dateien sind, werden in der Pause Schrauben zur Befestigung gesetzt, mittig der Aussparungen für ATX-Blende und Strombuchse.
Zuletzt werden mit einem 3mm Einschneider die Aussparungen ausgefräst und dann die Trennschnitte für die Teile ausgeführt.
Seitenteile, Bohrungen, Gewinde und Kühlrippen
In die Seitenteile aus Aluminium 286x70x8 mm werden vorn und hinten sowie oben und unten mit einem 2.5 mm Bohrer 6 mm tiefe Bohrungen eingebracht. Diese erhalten dann mit dem Gewindefräser ein 3 mm Innengewinde. Das Bohren wird mit dem Bohrzyklus G83 von LinuxCNC ausgeführt.
3 x 2 Seitenteile werden senkrecht in die Aussparung der Arbeitsplatte gestellt, ausgerichtet durch zwei Vierkant-Alustreben in 210 mm Abstand unter der Arbeisplatte. Für den zweiten Arbeitsgang, die Bohrungen und das Gewinde oben und unten werden dann 3 Seitenteile auf diese Streben gelegt.
Zuletzt zeigt das Video das Fräsen der Kühlrippen, was die Oberfläche der 8mm Seitenteile außen auf das 2,3-fache erhöht.
Ergebnis: Ein einsatzbereiter PC
Ein fertiger PC, Gehäuse pulverbeschichtet
Rückseite des fertigen PC mit Anschlüssen
Die ATX-Norm, Grundlage der Berechnungen für Grundplatte und Rückseite
Montage: Zusammenbau der Teile testen
Mainboard und ATX-Blende positionieren
ATX und Strom, Aussparungen auf der Rückseite
Fertiger PC mit Kühlblock und einem lüfterlosen Netzteil
Das Mainboard und der dreiteilige CPU-Kühlblock